The 4M's Approach to Management
- gicarconsultants
- Jan 26, 2021
- 3 min read
The 4Ms approach represents the pillar elements which influence on the result of any concerned process or project.
Any project manager or position related to the management of a team, project, production or process should be familiar with the traditional framework for viewing the resources available to a business, which can be useful when designing a business or project plan.
- Money
- Material
- Machine/Method
- Manpower
At some point in our career, we will be face with a complex project or a problem to solve; however, it is important to compose ourselves and return to the “basics”. The “Basics” we are speaking about here at the 4M approach, the simplest of tools which aid us on our journey to make every project successful and find a solution to any problem – a problem solver within our organization.
What is often a surprise to many people is how powerful this simple approach can be in solving operational problems by identification and eradication of the root cause(s) by those associates closest to the issues when and where they occur.
In general, the 4M-approach is widely used as a root cause analysis mechanics. However, in my experience, using these 4-pillars can also be utilized during the planning stage of a project in order to avoid future problems and implement a risk analysis approach. It can be utilized using past experiences or historic data to identify potential sources of variations, during continuous improvement development and undoubtedly risk analysis management. Remembering that these 4Ms are the core elements which drive project costs, schedule and quality.
Here are some examples of questions during the 4M-approach:
Money – Is the project budget relevant to the project scope? The budget is applicable to the other M’s including material, manpower, method and machinery.
Material – Has procurement process been established? - Do the materials meet the required specifications – Any foreseeable shortages? Is excess handling or movement reduced or eliminated? Are they stored appropriately?
Machine – Is the machinery reliable for the desired output, production and quality? Do breakdowns, defects or unplanned stoppages inhibit their ability to meet that goal?
Method - Do we have standard work methods in place which ensure and support consistent and safe production? This ties into the planned project schedule.
Manpower - Do our workers have the skill and motivation to do what is expected of them safely, consistently and effectively?
Ultimately, we use 4Ms to help structure the team’s thinking within the analyse phase of our standard framework for focused improvement. It secured the review of these project elements: Define, Measure, Analyse, Improve, Control.
Application – At GICAR CONSULTANTS, we strive to always simplify any management process. It is often the routine application of the 4Ms in a simple one-page format that best engages and enables the problem-solving capability needed to unlock the full potential of the organization.
Motivation – The GICAR CONSULTANTS blog presents topics which any management professional can be faced with in their daily practice. Ultimately, we strive to presents tools to help facilitate our approach. Simplicity always works best.
“Be a leader in your approach to management.”
Be a leader in your approach – include your entire project team in this approach and encourage their participation. Everyone’s contribution brings value!
Hope you enjoyed this post and hopefully can be useful to you and applicable in your practice.
Giovanni Carriero, ing.
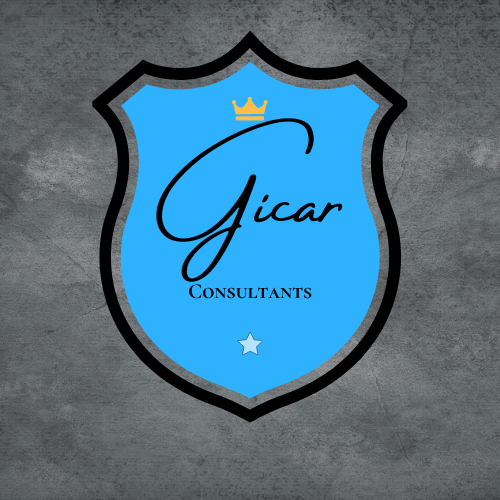
Comments